2022年11月に発表された汎用型AI(Chat-GPT)の話題が世界を席巻しています。産業界では製造現場にAI導入が始まり、製造現場の効率化や品質安定化等の事例が多数報告されています。
本記事では製造現場にAIを導入するメリットは何か?またどのような活用事例や成果が上がっているのかについて詳しく解説します。
1:製造現場でAIを導入するメリットは?
製造現場でAIを導入することで得られるメリットは以下の4つがあります。
1.業務効率化
2.人件費削減
3.安全性の向上
4.品質の安定化
1)業務効率化
AIを導入することにより、製造の要素(4M)、製造リードタイム、予知保全の改善が可能となります。
一般に、製造現場では「熟練のエンジニアによる経験や勘」に頼るマネージメントが中心でした。その主な重点テーマは以下の3点となります。
・製造の要素(4M)の最適化
・製造リードタイムの短縮
・予知保全の実施
従来は、これらの製造課題は、優秀な熟練エンジニアの頭の中にある経験(成功や失敗体験)や勘(経験から得られる眼力や慧眼)をもとに製造課題の解決が図られてきました。
今後は、過去のデータをAIに学習させて、確度の高い計画を作成することが可能となります。
2)人件費削減
AIを導入することにより、難易度の高い検査・作業を代替えし最適な必要人員を導き出します。
一般に「人による作業」では「作業手順書」(SOP)が作成され、その指示通りに製造作業が行われます。しかし、ある製造現場では熟練した作業員でしか対応できない検査・作業もあり、その検査・作業に対応できる人材の教育や確保が課題でした。
難易度が高い検査・作業行うためにAIで支援できるシステムを構築できれば、必要な作業員の削減が可能となります。
3)安全性の向上
AIを導入することにより製造現場の労働災害を極力「ゼロ」に近づけて、安全な職場環境をつくることができます。
一般に労働災害は、その障害の程度により「ハインリッヒの法則 (*1)」(経験則)に従うことが知られています。
●障害の発生割合⇒重大事故:軽微な事故:ヒヤリハット=1:29:300
これは、1件の重大事故の陰に、重大事故にならないに軽微な事故が29件隠れており、その陰に300件のヒヤリハット(冷やとしたり、ハッとした危険な事象)があることを示したものです。
重大事故を防止するためには、「危険個所」や「危険な動作」などを事前に洗い出し、どのようにコントロールするかが重要な課題となります。
例えば、AIと他の検査装置(カメラ等)を組み合わせたシステムを用いて、危険作業の監視を行うことで作業の安全性を確保することも可能となります。
4)品質の安定化
AIを導入することにより製造品質の安定化並びに出荷品質の向上を実現します。
製造現場の品質目標は、第一に製造工程の品質安定化、第二に不良を市場に流出しないことです。この2つの視点から品質安定化について説明します。
4-1)製造工程の品質安定化
製造現場では、さまざまな要因をコントロールすることで品質の安定化を実現します。
各種機械・装置の使用に際しては装置の生産条件を入力して制御する方法、人の作業は作業手順書(SOP)の使用が一般的でした。
化学プラント等の化学反応を伴う設備(*2)では、作業員の経験に基づく手動制御が採用されていました。しかし、手動制御の経験をAIに学ばせ、自律制御する事例が報告されています。
4-2)不良を市場に出荷しない取り組み(出荷品質の向上)
製造の最終工程では、製品に混入する不良品を人による検査などで検出除去します。
一般に人による目視検査では「微小な欠点(点やキズ等)」の検出や「動画表示の製品不具合(*3) 」は、見つけづらく不良流出のリスクがあります。そのためAIと画像認識などを組み合わせた検査システムを導入し、市場に流出する不良品の割合を限りなく「ゼロ」に近づける取り組みが行われています。
2:AI導入による業務効率化と活用事例
製造現場の業務効率化における課題とAIの活用
AIを導入した場合に、製造現場においてどのような業務効率化が行われ、どのような成果が期待されるのでしょうか?この章では具体的な事例を含めて、AIと製造現場での関係性と期待を説明します。
1)AI導入による総資産利益率の改善(*4)]
日本経済研究センターが作成した「日本企業のAI/Iotの導入状況」(2019)によれば、主に大企業ではAI導入の有無と、総資産利益率の間には正の相関があることが報告されています。
前述の報告は、AIを導入すると工場内や工場間の製造の要素(4M)を最適化することができ、効率の高い生産体制の構築を示しています。
4MとはMan(人)、Machine(設備・治工具)、Material(材料)、Method(方法)を示します。この4Mは、製造工程のオペレーションや品質管理を行うための重要なファクターとなっています。熟練の作業者やエンジニアは長年の経験から必要な4M(作業員数、装置台数、原材料・部品投入数など)の条件を導き出します。
ところが、これらの4M情報は、一部の限られた熟練作業者やエンジニアに偏ったり、情報が最新のものに更新されなかったりと、関係者が最新状況を共有できないケースがありました。また、これらの情報には、遊休設備、修理中設備等などの必要な情報がアップデートされていないケースも含まれていました。
最新の4M情報をデータベース化し、AIにより学習すれば最適な生産体制の構築が可能になります。
【活用事例】(*5)
タイヤ製造工場では、タイヤ成型工程は異なる部材を組み合わせて作るプロセスにAIを活用しています。この成型で使用するゴムは温度や生産条件により特性が変化するため、1人の作業員が貼り付いて管理する難しい工程でした。
AIの導入により、製造で得られるデータを分析し最適なアルゴリズムの生成を行います。その後、アルゴリズムによる製造工程の自動制御を実現し生産性は2倍に向上しました。
2)歩留まり改善や予知保全とAIの関連性
AIの導入は、各製造工程における歩留まり改善や設備の予知保全に貢献します。
2-1)製造工程の歩留まり改善
従来の製造現場では、熟練したエンジニアの経験と勘に頼る仕事の進め方が一般的でした。人に頼る方法は、特定の人にノウハウが蓄積され、標準化や技術伝承が難しい状況に陥ります。AIを導入すれば、過去の製造資料や歩留まり情報から学習を行い製造歩留まりの改善に寄与します。
【活用事例】(*6)
ある住宅建設会社では、木造住宅に使用する外壁材の生産に電子制御された高度なシステムを導入していました。しかし、原材料の大板からいろいろな形状に切り出す方法は人の経験によるため歩留まり改善には限界があります。
AIの導入による「最適な切り出し方法」で製造を行うと、従来に比べ歩留まりを0.3%改善できることが分かりました。
2-2)AIによる予知保全
必要部品をあらかじめ点検交換する方法には、一定の周期で実施する「定期保全」以外に、劣化部品の状態を定期的に点検し故障の兆候を見つける「予知保全」があります。
従来の予知保全では、熟練のエンジニアが装置の状況を確認して、属人的な経験や勘に基づき必要な部品を交換する方法が採用されてきました。
予知保全におけるAI活用では、作業点検時の故障前履歴(例えば、機器の稼働中のログ情報や、異常な振動など)のデータベースを作成し、故障パターンを学習させることで故障の予兆を検知することができるようになります。
今後は「定期点検のデータベース」からAIが故障の予兆を検知し、交換時期を判断して予知保全を行うことが可能です。
【活用事例】(*7)
ある化粧品会社の製造現場では、多くのバッチプラントや多数の品種数があり、監視作業員には高度なオペレーションが求められました。現在、従業員の世代交代により、経験が浅い監視作業員が少人数で多くの設備を品種ごとに管理するため、心理的負担が大きくなっていました。
この課題を解消すべく予兆段階で異常検知ができるAIを導入したことで、発生しつつある事象の検知や対処が短時間で出来るように変わりました。その結果、監視作業員の心理的負担の軽減が可能となりました。
3)製造リードタイムの短縮
AIを導入することで、生産開始から製品出荷までの製造リードタイムは短縮され、製造コストの削減や利益率の向上が期待されます。
「製造リードタイム」は、原材料や部品を製造工程に投入し、製造作業や検査を実施後、出荷までの全ての時間を合計したものです。
その中には、製造作業・加工・検査等の実際の作業に関わる時間だけでなく、工程途中の仕掛り在庫滞留時間、機械・装置のアイドリング運転等の作業準備時間、最終製品の出荷検査待ち時間などが含まれています。
【活用事例】(*8)
ある自動車用バックミラーメーカーでは、バックミラー(鏡)の表面キズ検査を、画像認識検査と人による目視確認で実施していましたが、検査精度に難がありました。特に、微小な点とキズの良否判定に技術課題を残していました。
そこでAIを導入し、良品と不良品の機械学習を行い、判定精度を高めることに成功しました。その結果を受けて全ラインにAIによる検査方法を展開し、製造の自動化へ移行しました。
3:AI導入による人件費削減と活用事例
製造現場の人件費削減における課題や、AIへの期待
産業界全体での人材確保の課題(生産人口減の推移)を明らかにします。その対策として、AIを導入した場合にどのような成果が期待されるのでしょうか?この章では具体的な事例を含めて、AI活用による製造現場での期待を説明します。
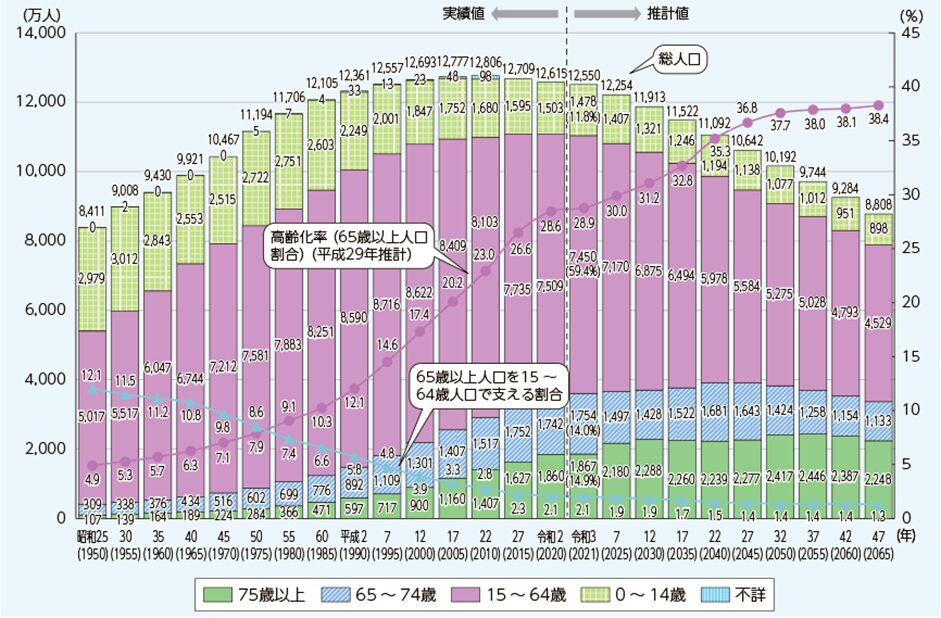
図1 高齢化の推移と将来推計
(出典)内閣府公表「令和4年版高齢社会白書」(*9)
内閣府公表「令和4年版高齢社会白書」によると、日本では「少子高齢化の進行」に伴い、2021年の生産人口(7,450万人)は、9年後の2030年では6,875万人となり、575万人(2021年から約8%減)減少します。さらに、2040年には5,978万人となり、1,472万人(2021年度から約20%減)減少します。
製造現場ではこの生産人口の減少により、単純作業者のみならず熟練エンジニア不足への対応が必要となります。定型作業や難しい作業の一部は、工程の自動化、ロボット化で対応するとしても、熟練エンジニアの知恵や経験はそのような置き換えはできません。そのためAIを使用して今までの経験を機械学習し、高度な判断と指示ができるように工場システムを進化させる必要があります。
同様に、高度な技術マネージメントエンジニア(技術部門長/工場長レベル)も減少が予測されるため、ますます人材の奪い合いとなります。また、技術の進展に伴い採用した人材の教育コスト(AI、AR、VRなどのIT技術)も年々増加することが予想されます。
したがって、製造現場の競争力を向上させるためには、現在の熟練エンジニアの知恵や経験をAIで置き換えることが一つの解決策となります。
【活用事例】(*11)
ある自動車メーカーでは、フロントハブ(自動車前部の車体と車輪をつなぐ部分)検査に外観目視検査と磁気探傷検査を実施していました。この検査は特殊な方法でキズを検出する熟練技能者のみができる検査です。
その後、AIによる熟練技能の技能を再現した検査方法を導入し、不良品と良品の判定精度を高めることに成功しました。
4:AI導入による安全性向上と活用事例
製造現場の安全性向上における課題や、AIへの期待
労働災害の現状とそこから導かれる課題について説明します。AIを導入した場合にどのような成果が期待されるのでしょうか?この章では具体的な事例を含めて、AI活用による製造現場での期待感を説明します。
表1. 業種、事故の型別死亡災害発生状況(2021年)(単位は件数)
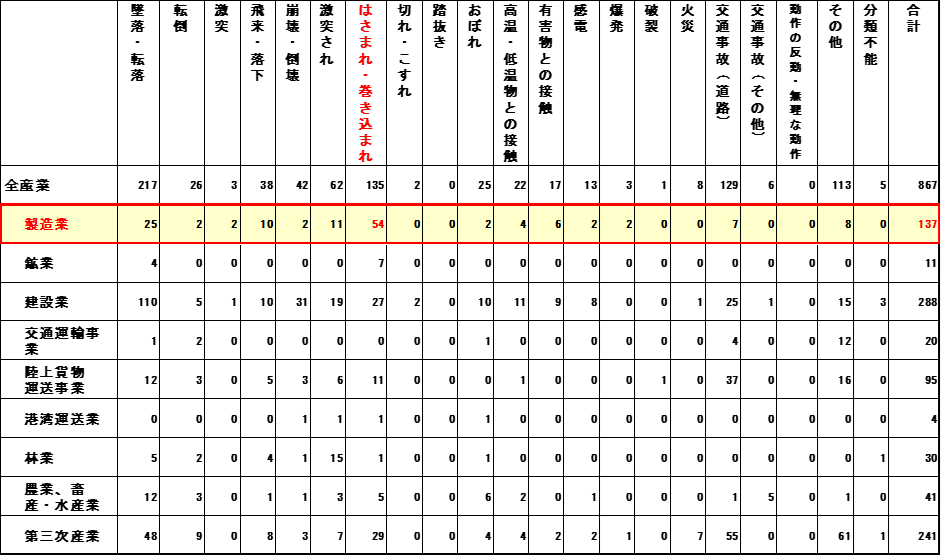
(出展)業種、事故の型別死亡災害発生状況(令和3年)–厚生労働省労働基準局安全衛生部安全課(*12)
図2.製造業における死亡事故の原因割合(表1の製造業のみ抽出)
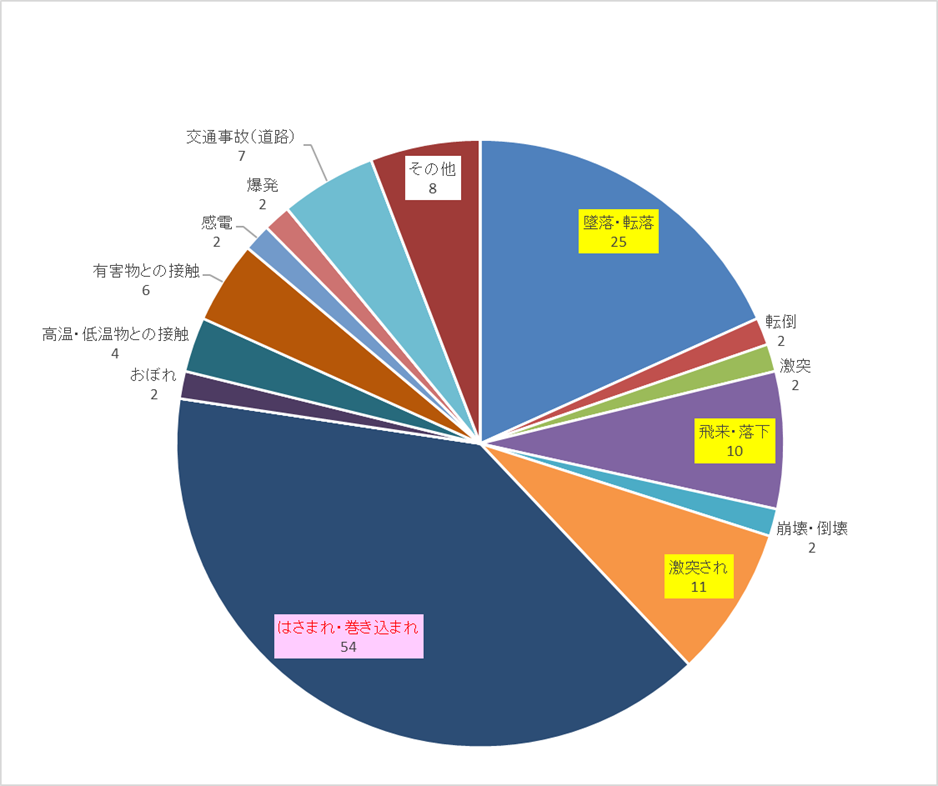
厚生労働省の「業種、事故の型別死亡災害発生状況(令和3年)」によると、2021年の全産業で発生した死亡事故867件の内、137件(16%)が製造業で発生しています。(表1参照)
製造業に限れば、死亡事故137件中54件(39%)が作業員の「はさまれ・巻き込まれ」が原因となっています。さらに件数の多い順では、第二位「墜落・転落」25件(18%)、第三位「激突され」11件(8%)、第四位「飛来・落下」10件(7%)となります。(図1参照)
表2. 業種、事故の型別死傷災害発生状況(2021年)(単位は件数)
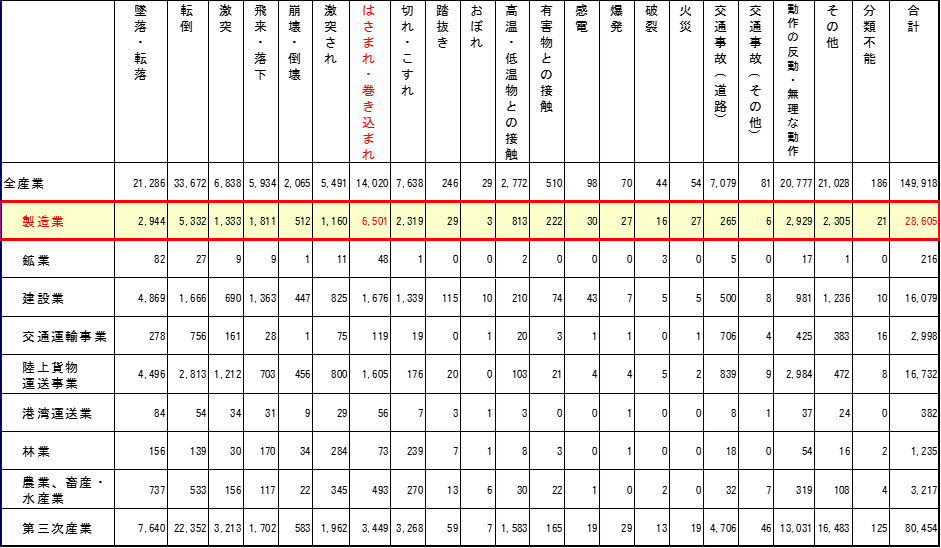
図3.製造業における死傷災害の原因割合(表2の製造業のみ抽出)
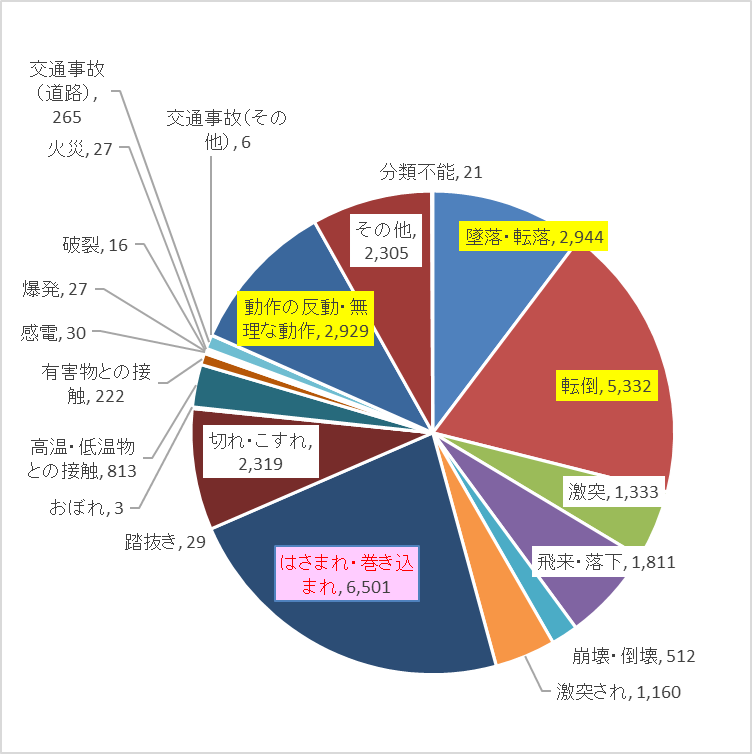
前述の資料によると、死亡事故より程度が軽い死傷災害では、全産業で発生した149,918件の内28,605件(19%)が製造業で発生しています。(表2参照)
製造業に限れば、死傷災害28,605件中6,501件(23%)が作業員の「はさまれ・巻き込まれ」が原因となっています。さらに件数の多い順では、第二位「転倒」5,332件(19%)、第三位「墜落・転落」2,944件(10%)、第四位「動作の反動・無理な動作」2,929件(10%)となります。(図3参照)
製造現場では、死亡事故や怪我などにつながる「危険個所」や「危険な動作」が多く潜んでいることが読み取れます。
死亡事故や死傷災害を詳細に分析し、どこに課題があり(または、有りそうか)を明確にする必要があります。さらに同資料には掲載されていない「ヒヤリハット事例」も製造現場ごとに情報収集することが求められます。
AIに過去の事故・災害データを学習させて活用することで、製造現場での安全確保を行うことができるようになります。
【活用事例】(*13)
ある鉄鋼メーカーでは、製鉄所の場所による明るさが異なり作業者の人物検知が困難な状況でした。
AIによる画像認識を導入することで、人物画像を機械学習し、実用レベルで人物検知が可能となりました。さらに、立ち入り禁止情報との連動を行い、禁止エリアに侵入した際は警報を鳴らしラインを停止するように変更しました。
5:AI導入による品質の安定化と活用事例
製造現場の品質安定化における課題や、AIへの期待
現在の製造現場の品質状況とそこから導かれる課題について「品質安定化」と「出荷品質向上」の観点から、AIへの期待と活用事例を説明します。
1)製造工程の品質安定化
製造現場での品質安定化を行うためには、不良品の発生工程を管理する必要があります。そのためには、どの工程で不良が発生するのかを「熟知する作業者」や「練達な装置操作ができるエンジニア」が求められていました。
AIを導入すれば、熟練の作業者やエンジニアに代って、安定した作業を長時間行い、作業自体を根本から改善できます。
【活用事例】(*14)
あるコンピューターのメーカーでは、産業ロボットの制御にAIを使用することが発表されました。このロボットの制御には自然言語処理が使用され、作業員がAIと対話しながらロボットを操作します。
この対話型AIは、数百ページに及ぶマニュアルを学び「熟練作業者」に代わる動作ができるようになっています。
2)不良を市場に出荷しない取り組み(出荷品質向上)
製造現場における作業員の目視検査には高い集中力が要求されます。その理由は出荷に混ざる不良品自体が顧客に迷惑をかけるだけでなく、企業そのものの信用に大きく影響するからです。
人による検査では、その習熟度合いや疲労の影響により、常に一定の作業品質を維持することが難しいです。特に人の目に頼る外観検査ではある一定の不良流出は考慮する必要があります。
AIを従来の検査方法と組み合わせれば、作業品質を保ちながら、長時間にわたり高精度の検査を実施することが可能となります。
【活用事例】(*15)
ある自動車用電装メーカーでは、メーター機器に液晶表示を使用しています。自動車機器の電子化に伴い液晶画面に動画を映すなど表示方法も変化していますが、この動画表示に不具合が生じた場合には、交通事故につながる危険が懸念されていました。
AIを導入することにより、この動画表示の画面でも的確に異常を除去できる検査方法を確立できるようになりました。
まとめ
製造現場にAIを適用するテーマは多々ありますが、その優先順位はどのようになるのでしょうか?
その答えの一つが「製造ラインの不等式」によるという考え方です。もう一つは、「企業利益追求」の考え方です。本記事では、2つの観点から取り組みの優先順位を説明します。
1)製造ラインの不等式による進め方
製造現場には、製造ラインの不等式なるものが存在します(*16])。これは、日常何か事態が起った場合の対応順位です。
それは、S>Q>D>C>Fで表されます。
ここで
・S:Safety(安全)
・Q:Quality(品質)
・D:Delivery(納期)
・C:Cost(原価)
・F:Fundamentals(企業体質)
S~Cは自明ですが、Fundamentalsはロット合格率、設備稼働率、製造歩留まり、原価率等となります。今後、このような製造に関する種々の指標についても順次AIによる指標改善が計られていくものと予想されます。
2)企業利益追求の進め方
企業の最終目標は利益をいかに確保するかということです。経営面から言えば製造原価を下げる施策は企業存続のために必要なテーマです。そのため原価改善につながる課題(例えば、業務効率化、人件費削減)は、優先的に取り上げられることとなります。
本記事が製造現場でのAI導入時の参考になれば幸いです。
出典:
(*1)ハインリッヒの法則
(*2)化学プラント等の化学反応を伴う設備
(*3)動画表示の製品不具合
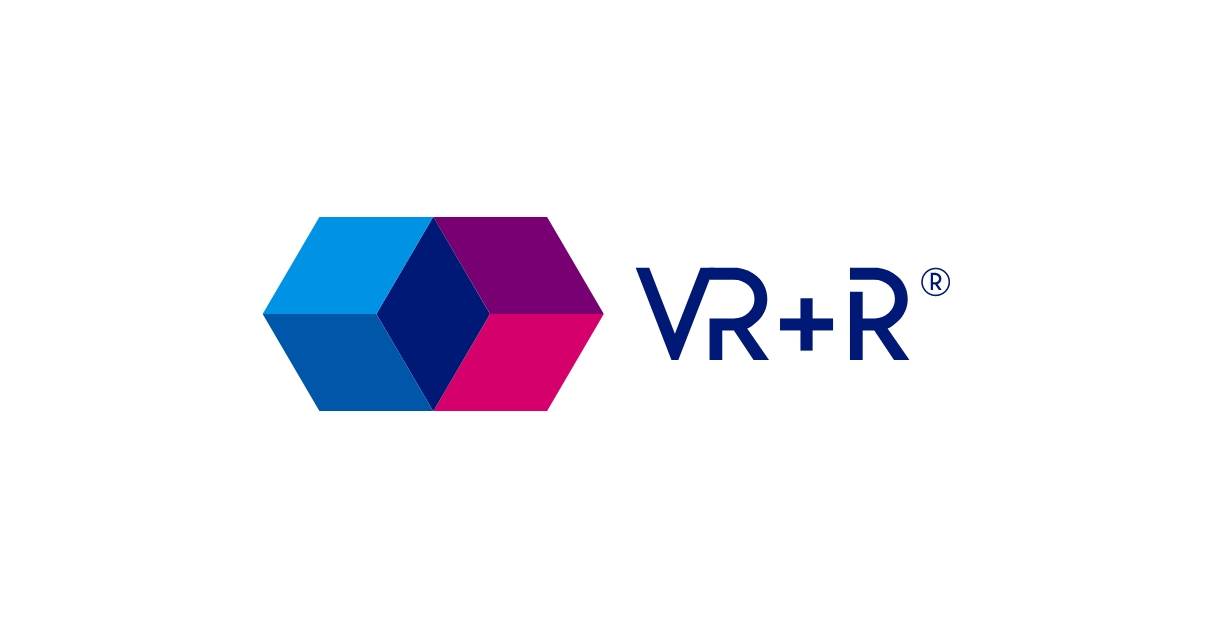
(*4)AI導入による総資産利益率の改善(日経研2019):
(*6)住宅外壁部材の板取最適化にAIを活用し、歩留まりを改善
(*7)オンライン異常予兆検知システムで時間的余裕の確保(花王/azbil)
(*9)内閣府(2022)「令和4年版高齢社会白書」
(*11)トヨタ自動車:「Deep Learningの専門知識を有するシーイーシーと
二人三脚でAIを育て上げることに成功。熟練技能が必要な磁気探傷検査を自動化することができました」
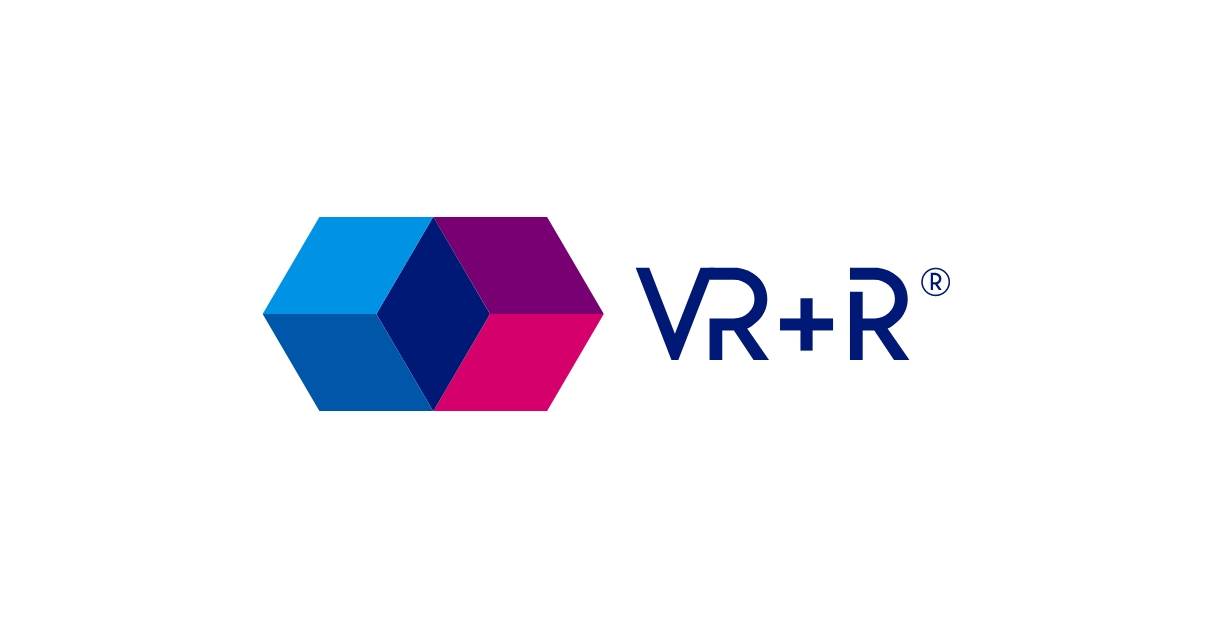
(*12)厚生労働省労働基準局安全衛生部安全課
(*13)JFEスチール:https://www.jfe-steel.co.jp/release/2018/12/181211.html
(*14)HPEの事例:https://monoist.itmedia.co.jp/mn/articles/2305/02/news081.html
(*15)デンソーの事例:https://www.brains-tech.co.jp/case/case22-denso/
(*16)参考:日立にみる「半導体工場の現場経営」P.43
コメント